Assembly Presses
Application: Heavy Truck U-Joint Assembly Press
Product: S-Series SMART Electro-Hydraulic Actuator
Challenge:
A Heavy Truck Axle manufacturer procured a horizontal assembly press machine for a new Axle line from a Special Machine Builder to replace an existing hydraulic press. The new line needed to achieve improved process quality for the assembly press machine station as part of a company-wide initiative to improve throughput and reduce rework.
In addition, the Axle manufacturer had a requirement to minimize the use of hydraulics in the plant due to the advantages of being environmentally cleaner, providing significant energy savings, reducing floor space and quieter operation.
The customers’ 'minimal hydraulics' mandate created unique challenges for the Machine Builder due to the high forces required in the assembly press stations.
Solution:
The Machine Builder considered using electro-mechanical actuators (EMA) but found that the large footprint and prohibitively expensive cost of EMA technology was and would not meet their project requirements. In addition, the builder had concerns about EMA screw life due to the uneven 'spike loads' the actuators would be subject to during production.
After careful consideration, the Machine Builder selected Kyntronics All-in-One SMART Electro-Hydraulic Actuator (SHA) for the horizontal assembly stations on the new Axle line. The SHAs were rated for 45,000 lbf (200kN) of force and were provided in a parallel configuration providing the force required in a compact package that fit the available space envelope.
The SHA provides precise and repeatable control of applied force and position which was critical for the quality standards required from the new assembly press machine. In addition, the SHAs utilized Rockwell Automation (Allen Bradley) Servo Motors and Drives which met the customer’s control specifications.
Results:
- The SHAs All-in-One feature eliminated the need for an HPU and hydraulic infrastructure on the new machine resulting in less space required for the machine, a clean working environment, quieter operation, and substantial energy savings.
- The SHA’s use of precision force and position control exceeded the Axle manufacturer’s stringent quality requirements and helped improve output of defect-free assemblies.
- The SHA provided very reliable, maintenance-free operation despite the uneven loads experienced during the assembly process.
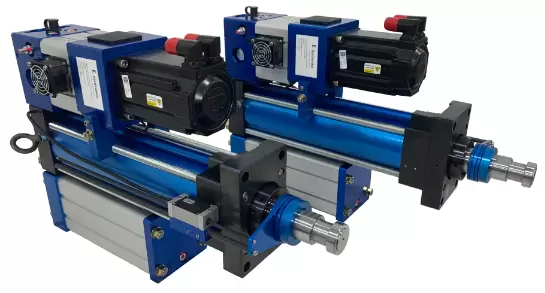
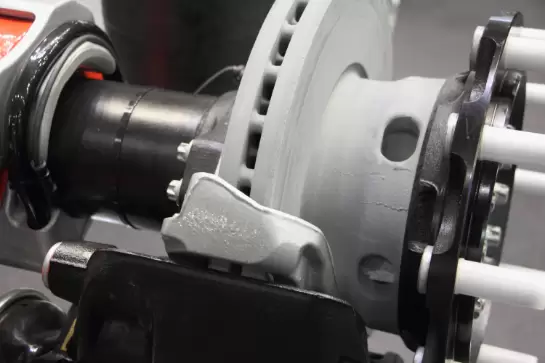